Working principle of MD roll (Patented in Japan/USA)
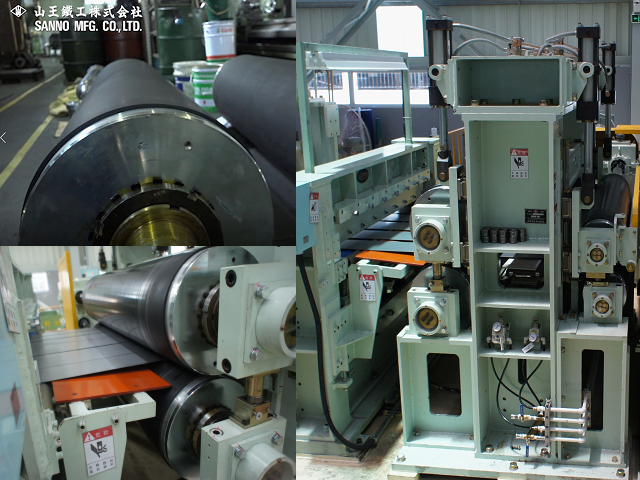
As you know, when cutting multiple strands on a slitter line, there is
a slight difference in the speed of each strand due to the difference in
coil winding outer diameter caused by the plate thickness deviation. If
this is captured instantaneously, the difference in velocity is expressed
as the difference in the amount of deformation of the elastic body.
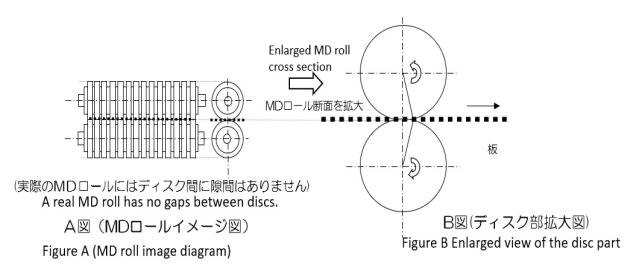
And the difference in deformation is proportional to the difference in
tension. In slitting, the thickness deviation of the product is about 2-3%,
so the speed difference for each line is also 2-3%. Therefore, the difference
in tension when the roll is braked is also 2-3%. (The line speed is the
actual diameter of the roll x π + the variable amount of the surface.)
Theoretically, it is as described above, but there are problems such as
the material of the elastic body, how to make grooves, depth, direction,
etc. there is. At our company, we produced a roll with vertical grooves
like the one above, but there were defects such as lateral vibration of
each disk-shaped tip due to the grooves, and it was not good for use. This
problem was resolved with the multi-disc type (a type in which many discs
are stacked). At our company, based on technical cooperation with STAMCO
in the United States, we have manufactured rolls of the horizontal groove
type, but theoretically they are exactly the same as the above. However,
there was a problem with the bouncing sound of the grooves, so in order
to solve this problem, we completed the "MD Roll" through the
above process.
Loop slitter and loopless slitter
Slitter lines for metals are roughly divided into the following two types. 1) Loop type slitter 2) Loopless type slitter (tight type) Each has the following advantages/disadvantages. Selection is based on the size of the coil to be slit (coil weight, coil outer diameter, coil width), slit content, installation environment, etc.
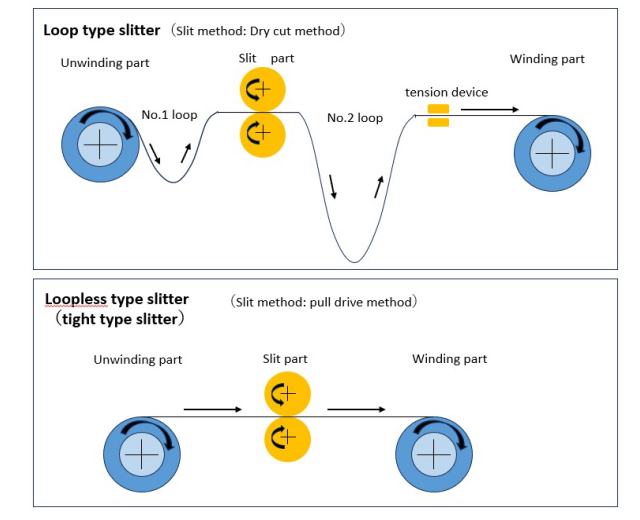
1) Since the loop slitter has loops before and after the slitting part, slitting can be performed without being affected by tension in the front and back during slitting. You can do it. In addition, unlike tight slitters, it is not affected by the size of the coil, so it is widely used for slitting small to large coils of iron/stainless steel/aluminum/wrought copper and other base materials/small pieces. Compared to the tight type, the installation area of the device is large, and the installation cost is high due to the need for pit construction. In terms of productivity, unlike the tight-type winding machine, there is no winding machine such as a winding machine, and the drum is used for winding, so there is no setup time required for setting/removing the winding machine, and there are no weight restrictions. The advantage is high productivity.
2) Tight type requires precise control of tension and speed in order to
maintain slitting quality because there is tension on the entry side and
tension on the exit side before and after the slit. Therefore, it is not
suitable for large coils and is often used for slitting small and medium-sized
coils less than 10 tons in width and less than 1000 mm in width. It is
used for slicing copper products and stainless steel, and for slitting
foil. Disadvantages are that a special winding shaft/winding tool is required
to absorb the plate thickness deviation after slitting, and that there
are restrictions on the width and weight of the winding coil. The advantage
is that the introduction cost is relatively low because there is no need
for installation space / pit construction, and thin materials and narrow
slits can be made because the board thickness deviation is absorbed by
the winding shaft / winding jig tool.