MDロールの作動原理 (日本/米国で特許取得)
1. MDロールとは?
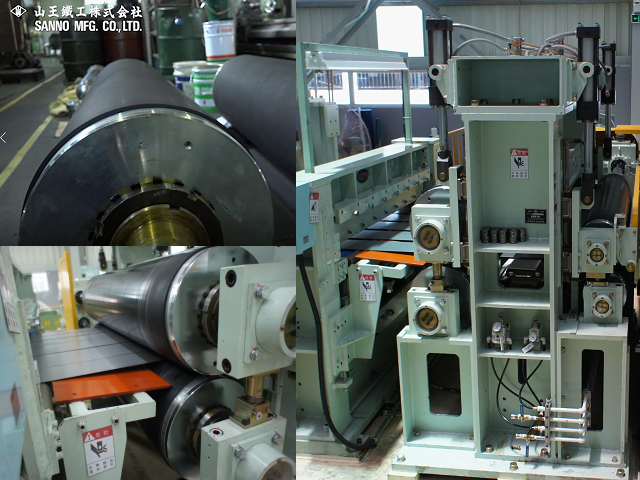
作動原理を簡単に説明するために、A図のようなゴムロールに3㎜位の縦溝を入れたロールを考えて下さい。
B図のように、ロールの間に薄板をはさんでロールにブレーキをかけて引っ張ると、板に張力がかかり、ロールの表面は図のように変形をおこしながら回転します。その際の変形量(ゴムのたわみ量)は張力に比例します。
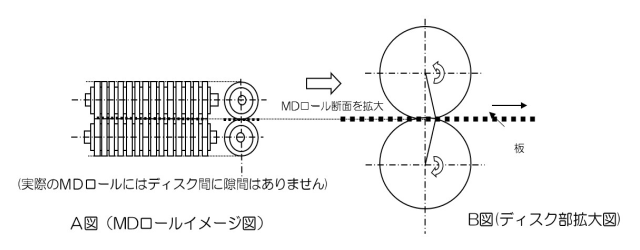
ご承知のように、スリッターラインにおいて多条で切断した場合、板厚偏差によるコイルの巻取り外径の差により、各条の速度に微妙な差があります。
これを瞬間的にとらえると、その速度の差は、弾性体の変形量の差となって表されます。
そして、変形量の差は張力の差と比例します。
スリット加工においては、製品の板厚偏差は、おおよそ 2~3% ですから各条との速度の差も 2~3% となります。
よって、ロールにブレーキがかかった状態での張力の差も 2~3% となる訳です。
(ライン速度は、ロールの実際の直径 × π + 表面の変計量となります。)
理論的には、以上の通りでありますが、弾性体の材質、溝の入れ方、深さ、方向等の問題があります。
弊社では、上記の様な縦溝のロールを製作しましたが、各円板状の先端が溝によって横振れする等の欠点が表れ、使用上は不調でありましたので研究/実機TESTを繰り返し現在のマルチディスク型(円板を多数積層する型式)で解決しました。
弊社では、従来、米国・STAMCO社との技術提携に基き、横溝型の ロールを製作してきましたが、理論的には全く上記のものと同一であります。
ただ、溝の跳ね返る音等に課題がありましたので、弊社ではこの問題を解決する為に以上のような経過を経て 『 MDロール 』 を完成させました。
ループスリッタとループレススリッタ
金属用スリッターラインは、大きく分けて次の2つのタイプのスリッターラインが使用れております。
1)ループタイプ スリッター
2)ループレスタイプ スリッター(タイト式)
各々以下の様なメリット/デメリットがあります。
スリットするコイルの規模(コイルの重量、コイル外径、コイル幅)、スリット内容、設置環境等により選択されております。
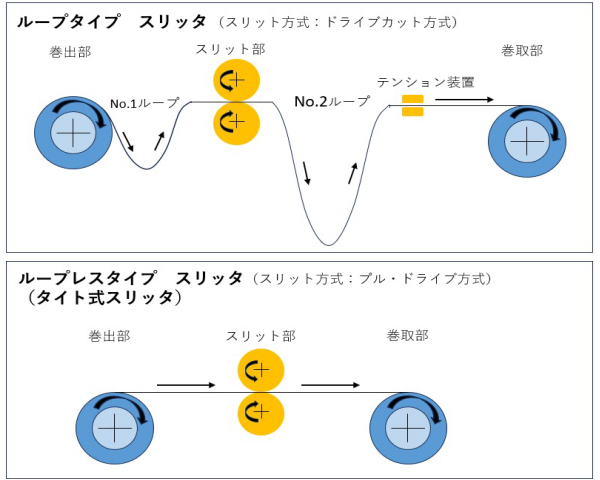
1)ループスリッタは、スリット部の前後にループがあるため、スリット時に前後の張力の影響を受けないでスリットが行える為、カッタ刃と材料の速度が同速でスリットされ為良好なせん断加工が行えます。
またタイトスリッタの様にコイル規模に影響されない為、小型から大型コイルの鉄/ステンレス/アルミニウム/伸銅品等のスリットで広く使用されています。
タイト式と比較し、装置の設置面積が大きく、ピット工事が必要な為導入コストが高くなる点/設置面積がデメリットとなります。 生産性に関しては、タイト式の様な巻取盤等の巻取治工具を使用せずドラムで巻き取る為、巻取治工具のセット/撤去作業等段取り時間が不要でかつ巻取コイルの重量制限も無い為生産性が高いことがメリットです。
2)タイト式は、スリット部の前後に入側張力・出側張力が存在する為、スリット品質を保つ為に張力と速度の緻密な制御が要求されます。
その為、大きなコイルは不得意で10tonに満たない、1000mm幅以下の中小規模なコイルのスリットで使用されることが多い方式です。 伸銅品やステンレスの小割、箔のスリットで使用されております。 スリット後の板厚偏差を吸収する為に特別な巻取軸/巻取治工具必要であること、巻取コイルの幅や重量に制限があることがデメリットとなります。 設置スペース/ピット工事が不要な為、導入コストが比較的安価なこと、板厚偏差を巻取軸/巻取治工具で吸収する為、薄い材料(巻取り距離の長いコイル)や細幅のスリットが行えることがメリットです。